Why Regular Packaging Machine Repair Is Essential for Your Business
Why Regular Packaging Machine Repair Is Essential for Your Business
Blog Article
Quick and Reliable Product Packaging Device Repair Work Provider to Minimize Downtime
In the affordable landscape of production, the performance of product packaging procedures pivots on the integrity of machinery. Quick and trusted repair service services are crucial in alleviating downtime, which can lead to considerable functional obstacles and financial losses.
Relevance of Timely Repairs
Prompt fixings of packaging makers are important for preserving functional effectiveness and reducing downtime. In the fast-paced environment of manufacturing and product packaging, even small malfunctions can lead to substantial hold-ups and efficiency losses. Addressing concerns promptly makes sure that devices run at their optimum capability, consequently protecting the flow of operations.
Furthermore, regular and prompt maintenance can prevent the escalation of small issues into significant failures, which typically incur higher fixing prices and longer downtimes. An aggressive strategy to equipment fixing not only maintains the stability of the equipment however additionally enhances the general dependability of the assembly line.
Furthermore, prompt repairs add to the longevity of packaging equipment. Machines that are serviced promptly are less likely to struggle with extreme wear and tear, permitting businesses to maximize their investments. This is particularly crucial in markets where high-speed packaging is vital, as the need for regular efficiency is paramount.
Advantages of Reliable Company
Trustworthy company play a pivotal function in guaranteeing the smooth procedure of product packaging equipments. Their know-how not just enhances the efficiency of repair work however also contributes dramatically to the durability of devices. Reputable solution carriers are geared up with the technological knowledge and experience essential to detect concerns accurately and apply effective options swiftly. This minimizes the risk of recurring problems and guarantees that devices operate at ideal performance levels.

Furthermore, a credible company supplies detailed support, including training and assistance for personnel on equipment procedure and maintenance finest techniques. This not just empowers employees however additionally cultivates a society of security and efficiency within the company. Overall, the benefits of engaging reputable provider expand past instant repair work, positively influencing the entire operational workflow of product packaging procedures.
Usual Packaging Machine Concerns
In the world of packaging procedures, numerous issues can jeopardize the effectiveness and performance of equipments. One common problem is mechanical failing, usually coming from deterioration or inadequate maintenance. Components such as gears, belts, and motors might stop working, resulting in breakdowns that halt manufacturing. An additional typical problem is misalignment, which can create jams and uneven product packaging, impacting item high quality and throughput.
Electric troubles can additionally disrupt packaging operations. Damaged electrical wiring or malfunctioning sensors may lead to irregular device actions, causing hold-ups Recommended Site and increased functional prices. In addition, software program glitches can hinder the equipment's programming, leading to operational inadequacies.
Irregular product circulation is one more vital problem. This can emerge from variants in item weight, dimension, or shape, which might affect the maker's capability to deal with things properly. Lastly, insufficient training of operators can aggravate these problems, as untrained employees might not acknowledge very Continued early indications of malfunction or may abuse the devices.
Dealing with these usual product packaging maker problems immediately is vital to maintaining performance and making sure a smooth procedure. Regular evaluations and proactive maintenance can significantly minimize these problems, cultivating a reliable packaging setting.
Tips for Reducing Downtime
To reduce downtime in packaging procedures, carrying out a proactive upkeep method is important. Consistently set up maintenance checks can determine possible issues prior to they escalate, guaranteeing equipments run effectively. Developing a routine that includes lubrication, calibration, and inspection of critical parts can dramatically decrease the regularity of unforeseen break downs.
Training personnel to run machinery appropriately and identify very early indication of breakdown can additionally play a vital function. Equipping drivers with the knowledge to do standard troubleshooting can stop small problems from creating major delays. Additionally, maintaining an efficient stock of crucial extra parts can quicken fixings, as awaiting components can bring about extended downtime.
In addition, recording equipment efficiency and maintenance activities can aid identify patterns and frequent issues, permitting targeted interventions. Integrating sophisticated monitoring modern technologies can provide real-time data, allowing predictive maintenance and lessening the risk of sudden failures.
Last but not least, fostering open interaction in between drivers and maintenance teams makes certain that any kind of abnormalities are quickly reported and addressed. By taking these proactive procedures, services can enhance functional effectiveness and significantly minimize downtime in product packaging procedures.
Choosing the Right Repair Service Service
Selecting the appropriate repair solution for packaging machines is an important decision that can considerably affect functional performance. An appropriate company ensures that your machinery is fixed promptly, effectively, and to the highest possible standards. Begin by reviewing the copyright's experience with your particular sort of packaging equipment. A technician aware of your equipment can diagnose issues more properly and apply remedies more quickly.
Next, consider the company's online reputation. Seeking comments from various other businesses within your sector can give insights right into reliability and quality. Qualifications and collaborations with acknowledged tools producers can likewise suggest a commitment to quality.
Additionally, evaluate their action time and schedule. A company who can provide prompt assistance lessens downtime and keeps manufacturing flow stable. It's likewise crucial to inquire concerning service warranty and service guarantees, which can reflect the self-confidence the provider has in their work.

Final Thought
In verdict, the relevance of fast and reliable product packaging device repair work services can not be overstated, as they play an important function in decreasing downtime and making certain functional efficiency. By focusing on prompt fixings and selecting dependable provider, companies can properly resolve typical problems and keep efficiency. Applying proactive upkeep practices and investing in personnel training additional boosts the long life of product packaging equipment. Eventually, a tactical approach to fix services cultivates a much more resilient manufacturing atmosphere.
Timely repair work of packaging equipments are crucial for preserving operational efficiency and minimizing have a peek at this site downtime.Furthermore, prompt repair work add to the longevity of product packaging machinery. In general, the benefits of involving reliable service companies prolong past prompt repair work, favorably impacting the whole operational operations of packaging processes.
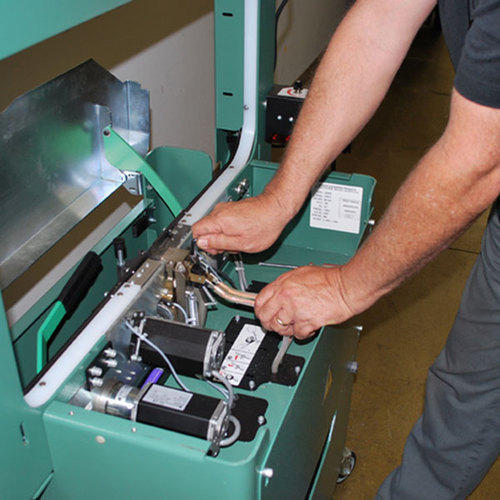
Report this page